Retrofitting für die vernetzte Produktion
- Written by Redaktion
- font size decrease font size increase font size
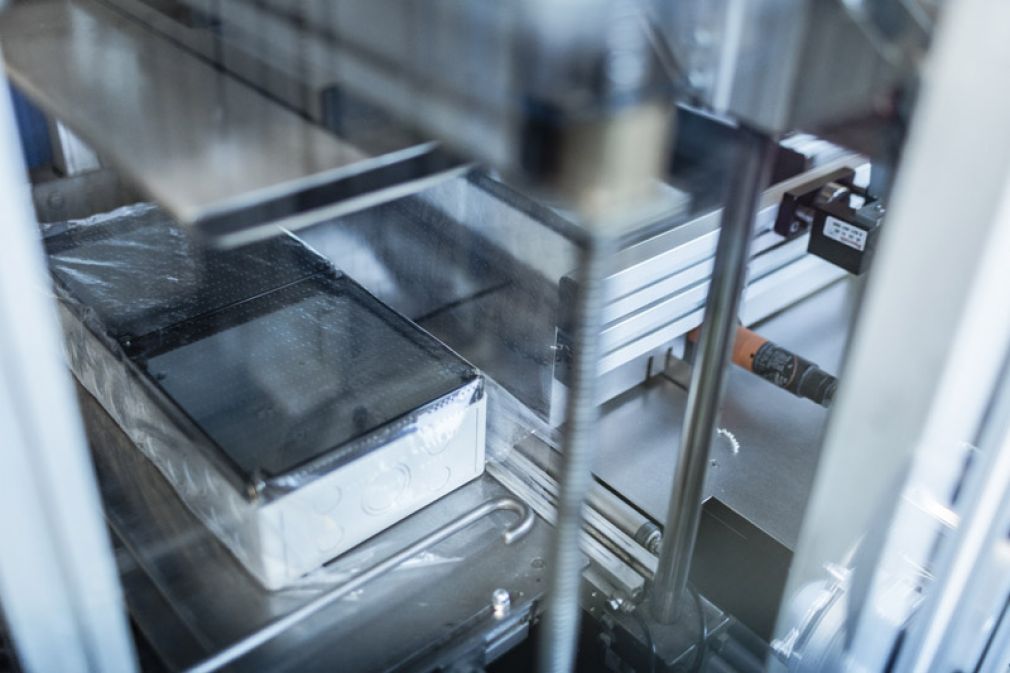
Mittelständische Unternehmen stehen oft vor der Frage, wie sie die Reise zur intelligenten Fabrik strategisch anlegen sollen. Ein Retrofit-Stufenmodell empfiehlt vier Etappen dazu.
Um den Umstieg in die neue Ära der vernetzen Maschinenwelt zu schaffen, stehen Unternehmen grundsätzlich zwei Wege offen: Beim Greenfield-Ansatz werden Maschinen der neuesten Generation angeschafft, was für viele Betriebe jedoch wirtschaftlich nicht vertretbar ist. Der Brownfield-Ansatz – im Industriebereich auch unter dem Namen »Retrofitting« bekannt – bezeichnet eine andere Methode: Dabei werden ältere Maschinen nachträglich modernisiert beziehungsweise aufgerüstet, um sie an digitale Systeme anzubinden. Die massiven Investitionskosten und der oft hohe Schulungsaufwand des Greenfield-Ansatzes entfallen hier.
So funktioniert Retrofitting im Industriebereich
Ein wesentlicher Vorteil von Retrofitting ist, dass die Methode schrittweise umgesetzt werden kann. Die Bandbreite reicht von der intelligenten Überwachung einzelner Maschinen bis zur unternehmensweiten Datensammlung für neue Geschäftsmodelle. Der Verband Deutscher Maschinen- und Anlagenbau hat gemeinsam mit Fraunhofer ein Retrofit-Stufenmodell entwickelt. Zu den wichtigsten Schritten gehören:
1. Messgrößen definieren. Hier geht es darum, je nach Use Case relevante Werte einer Maschine oder eines Maschinenparks zu bestimmen. Diese reichen von den Umgebungsbedingungen über Vibrations- und Bewegungsdaten bis hin zu prozessspezifischen Messgrößen.
2. Vorhandene Datenquellen oder externe Sensorik nutzen. Je nach Alter und Ausbaustufe kann es sein, dass eine Maschine die erforderliche Sensorik und entsprechenden Schnittstellen wie etwa Ethernet enthält oder diese sich leicht nachrüsten lassen. Der Kontakt zum Hersteller erspart oft lästigen Zusatzaufwand. Wenn dies nicht möglich ist, ist der Einsatz von externer Sensorik notwendig. Hier sind Lösungen in Entwicklung, die die geringen Fertigungskosten der Sensoren in der Consumer-Elektronik oder Automobilbranche mit den hohen Anforderungen im Industriebereich zu verbinden versuchen.
3. Digitale Kommunikation ermöglichen. Zu diesem Themenkomplex gehört etwa die Überprüfung der Netzwerkinfrastruktur inklusive erforderlicher Bandbreiten sowie die Übersetzung der Sensordaten, falls diese nicht bereits in einem Industrie 4.0-Format vorliegen. In der Regel übernehmen dies Industrial Internet of Things (IIoT) Gateways oder Industrie-PCs (IPC).
4. Datenanalyse und -aufbereitung sowie daraus abgeleitete Aktionen einrichten. Hier geht es darum, die Daten so zu nutzen, dass etwa die Maschinen weitgehend automatisiert überwacht und mögliche Störfälle frühzeitig erkannt werden – Stichwort »Predictive Maintenance«. Um das Ziel der optimalen Effizienz einer Brownfield-Anlage zu erreichen, kommen zunehmend Technologien wie Künstliche Intelligenz beziehungsweise Machine Learning in Verbindung mit ERP als zentrale Datenplattform und digitales Rückgrat im Produktionsumfeld zum Einsatz.
proALPHA hat in einem Proof of Concept-Projekt bei Spelsberg, einem Hersteller von Kunststoffgehäusen für Elektrotechnik und Industrie, einen Prototyp auf Basis eines Raspberry Pi entwickelt. Dieser empfängt, verarbeitet und leitet Produktionsbefehle vom ERP-System an die Maschine weiter. Gemeinsam mit dem Pilotkunden erarbeitete das Team außerdem ein Konzept für einen Rückkanal, der einen Informationsfluss von der Maschine an proALPHA ERP ermöglicht.
Fazit: Mittelständische Unternehmen im Produktionsumfeld haben mit Retrofitting und einem intelligenten ERP-System eine Methode an der Hand, die den Umstieg in die digitale Ära deutlich vereinfacht und beschleunigt.