Best of Cobots
- Written by Redaktion
- font size decrease font size increase font size
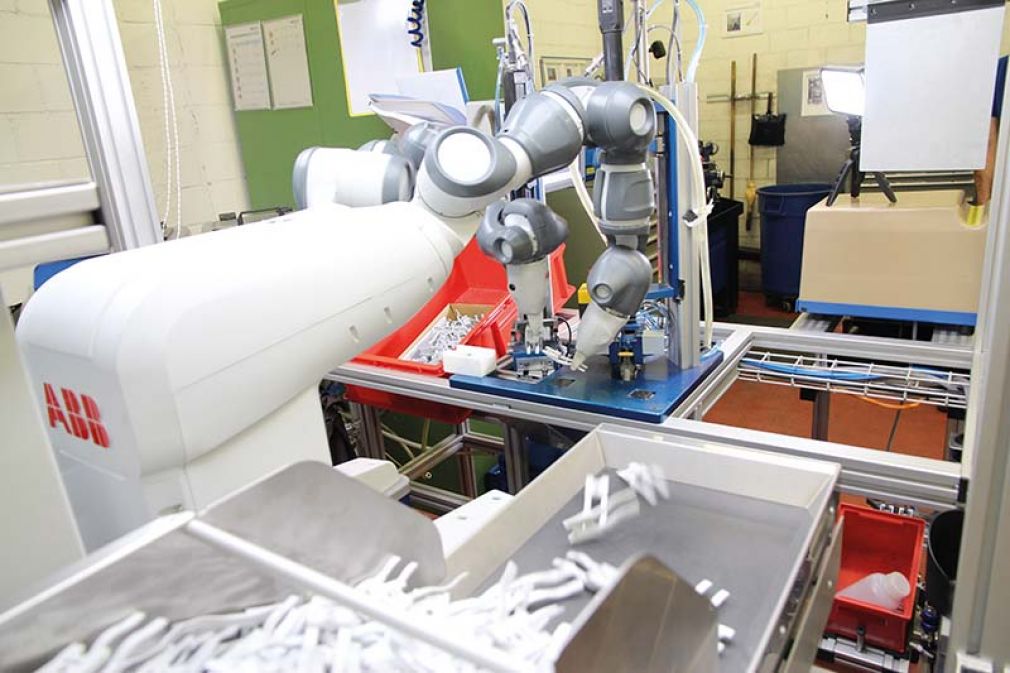
Gelungene Beispiele für Einsätze von kollaborativen Robotern zur Montage in der Möbelindustrie, Materialversorgung in der Fabrik, Qualitätskontrollen und für Verpackungsaufgaben.
ABB: Hawa Sliding Solutions
Der Montagevorgang wirkt reichlich monoton: Mit der linken Hand ein Teil greifen, mit der rechten das Gegenstück dazu, passend aufeinanderlegen, dann nacheinander in die zwei vorgelagerten Verschraubsysteme einführen. Und fertig ist das Stopperelement für Schiebetüren. Bei Hawa Sliding Solutions in Sirnach im Schweizer Kanton Thurgau ist seit dem Frühling 2017 »YuMi« von ABB im Einsatz. Der Cobot bewährt sich beim autonomen Zusammenfügen von Kleinteilen für Schiebebeschläge für Möbel und ist mit einer Handhabungskapazität von maximal 500 g pro Arm für sehr leichte Teile geeignet. YuMi ist für die sichere Kollaboration mit Menschen konzipiert. Registriert er einen unerwarteten Kontakt, stoppt er seine Bewegungen binnen Millisekunden. Die weiche Schutzpolsterung ist so aufgebaut, dass ein Einklemmen von Körperteilen ausgeschlossen werden kann.
Die Programmierung des Roboters wird beim Kunden selbst geleistet. »Wir haben ein Automatisierungsteam aus Mitarbeitern beider Standorte gebildet, das sich das nötige Know-how – ohne große Vorkenntnisse – in Schulungen bei ABB angeeignet hat«, berichtet Henri Schildknecht, Teamleiter Werkzeugbau bei Hawa Sliding Solutions. In die Greifer des Roboters können optional Kameras integriert werden. Das ermöglicht eine Führung der Roboterhand durch Bildverarbeitung. Die integrierten Kameras werden zusätzlich zur Qualitätskontrolle eingesetzt. Künftig soll YuMi in der Produktion weitere Montageaufgaben übernehmen.
Kunde: Hawa Sliding Solutions AG
Besonderheit: Der Einsatz des Cobots ist auf Flexibilität ausgerichtet. YuMi, 38 kg leicht, lässt sich innerhalb von Minuten von seinem Arbeitsplatz entfernen und per Tastendruck mit einem anderen Programm an anderen Stationen einsetzen.
Hintergrund: Der mittelständische Kunde zählt zu den ersten Unternehmen der Schweiz, die den Zweiarm-Roboter von ABB einsetzen – für Wachstum und die langfristige Sicherung des Produktionsstandorts.
Buxbaum Automation: Philips Austria, EM Technologies, Omron
Philips produziert in Österreich jährlich mehr als 20 Millionen Schneidelemente für Haar- und Bartschneidegeräte. Für interne Materialtransporte werden seit geraumer Zeit autonom fahrende, mobile Transportroboter (AMR) von Omron eingesetzt. Ziel eines Projekts war es, die OEE-Werte (»Overall Equipment Effectiveness«) der vollautomatischen Montagelinien zu erhöhen. Durch die Umstellung von einer diskontinuierlichen, manuellen Materialversorgung auf eine automatisierte, kontinuierliche Versorgung konnte der WIP (»work in progress«) von Tagen auf Stunden reduziert werden. Dabei wurde auch der Bedarf an Transportgebinden um den Faktor zehn reduziert. Neben den klassischen Transportfunktionen wird das AMR nun auch das Aktivieren, Abschließen von Prozessschritten und das Buchen von Aufträgen übernehmen.
Dabei wird die Kommunikation nicht nur zwischen Roboter und Maschine, sondern auch zwischen Mensch und Roboter aktiv erfolgen. So werden aus Sicherheitsüberlegungen Abfahrten vorangekündigt und der Mitarbeiter sprachlich über die vorherrschende Situation informiert. Hindernisse werden erkannt und durch alternative Routengestaltung umfahren. Die Koordination mehrerer AMR inklusive Lademanagement erfolgt ebenso autonom.
Kunde: Philips Austria, EM Technologies
Umfang: autonom fahrende, mobile Transportroboter in Montagehallen für die Versorgung der Linien mit Material.
Hintergrund: Ausschlaggebend für die Wahl des Produktes war die einfache Bedienung, eine relativ hohe Transportgeschwindigkeit und die Funktionssicherheit in engen Bereichen in der Halle.
Universal Robots: Melecs EWS
Melecs ist der größte österreichische Elektronikfertigungs-Dienstleister mit einem Umsatz von 260 Mio. Euro pro Jahr, ein Global Player in der Automobilindustrie und marktführend im Bereich Allradgetriebe-Steuerungen. Im Elektronikwerk in Siegendorf wurde ein Cobot eingerichtet, um kosteneffizienter und schneller automatisieren zu können. In Zusammenarbeit mit Fraunhofer Austria Research wurde ein UR5 von Universal Robots als Ergänzung zu den bereits laufenden Industrierobotern und Anlagen installiert.
Der Roboter übernimmt die Verpackung von Elektronikbauteilen für Wasserpumpen in Fahrzeugen. Das Handling der kleinen, runden Leiterplatten mit einem Durchmesser von rund 4 cm wurde zuvor im Dreischichtbetrieb manuell durchgeführt. Jetzt verpackt der kollaborierende UR-Roboter Seite an Seite mit den Mitarbeitern rund zwei Millionen Leiterplatten pro Jahr. Diese Bauteile finden am Ende der Lieferkette ihren Platz in den unterschiedlichsten Modellen von VW, BMW, Mercedes und Co.
»Die erfolgreiche Umsetzung einer Mensch-Roboter-Kooperation mit einem UR-Cobot in unserer Fertigung resultierte in einer zuverlässig und hochwirtschaftlich laufenden Anlage sowie in verbesserten Arbeitsbedingungen für unsere Produktionsmitarbeiterinnen und Mitarbeiter«, sagt Georg Loisel, VP Quality Management and Production System bei der Melecs-Gruppe.
Kunde: Melecs EWS GmbH mit dem Elektronikwerk Siegendorf der Unternehmensgruppe
Effekte: Die Produktivität der Fertigungsinsel in Siegendorf ist um 25 % gestiegen. Das Einbinden des Präzisions-Cobots in den Verpackungsprozess sichert nicht nur die Qualität der Bauteile – damit lassen sich außerdem die geforderten, sehr kurzen Taktzeiten von fünf bis sechs Sekunden Verpackungszeit pro Baugruppe einhalten.
Flexiblität: Die einfache Handhabung des UR5 ermöglicht den Ingenieuren bei Melecs, Projekte direkt und ohne langwierigen Programmieraufwand zu realisieren.
Rockwell Automation: Automotive-Industrie
Rockwell Automation unterstützt mit Cobots von Herstellern wie KUKA und Universal Robots auch die Zulieferindustrie der Automobilbranche. Bei zwei Herstellern von Autositzen mit Standorten in Schweden, der Slowakei und Tschechien wurden spezialisierte Testbereiche in der Produktion ausgerüstet. »Die finale Qualitätskontrolle ist der letzte Schritt in einer Fertigungslinie.
Dort sind die Cobots im Einsatz«, erklärt Andreas Schlipf, Leiter des Teams für End-of-Line-Testing bei Rockwell Automation. Zum Einsatz kommen kollaborative Roboter in unterschiedlichen Konstellationen mit der entsprechenden Sicherheitstechnik, die etwa ein Verlangsamen bei einer Annäherung oder ein sofortiges Stoppen bei einer Kollision einleitet. Die Cobots, die zu den Qualitäts- und Funktionstest der Elektronik und manuellen Bedienung der Sitze eingesetzt werden, greifen mit Multifunktionstools Steckverbinder und Kabel für das Anschließen in der Testumgebung, drücken Knöpfe und prüfen bei Premium-Ausführungen von Sitzen auch mit Luftstrommessgeräten integrierte Ventilatoren.n
Kunden: Hersteller in der Automobilzulieferindustrie
Umfang: Zahlreiche Fertigungslinien an Standorten von Herstellern in Schweden, Slowakei und Tschechien.
Besonderheit: Die Cobots sind rund um die Uhr im Einsatz. Die Taktung eines Tests beträgt lediglich 65 bis 68 Sekunden – in dieser Zeit wird der Autositz per Kabel angeschlossen, es werden alle Knöpfe und Hebel manuell bewegt und sämtliche Funktionalitäten gemessen und getestet.