Neu denken am Bau
- Written by Karin Legat
- font size decrease font size increase font size
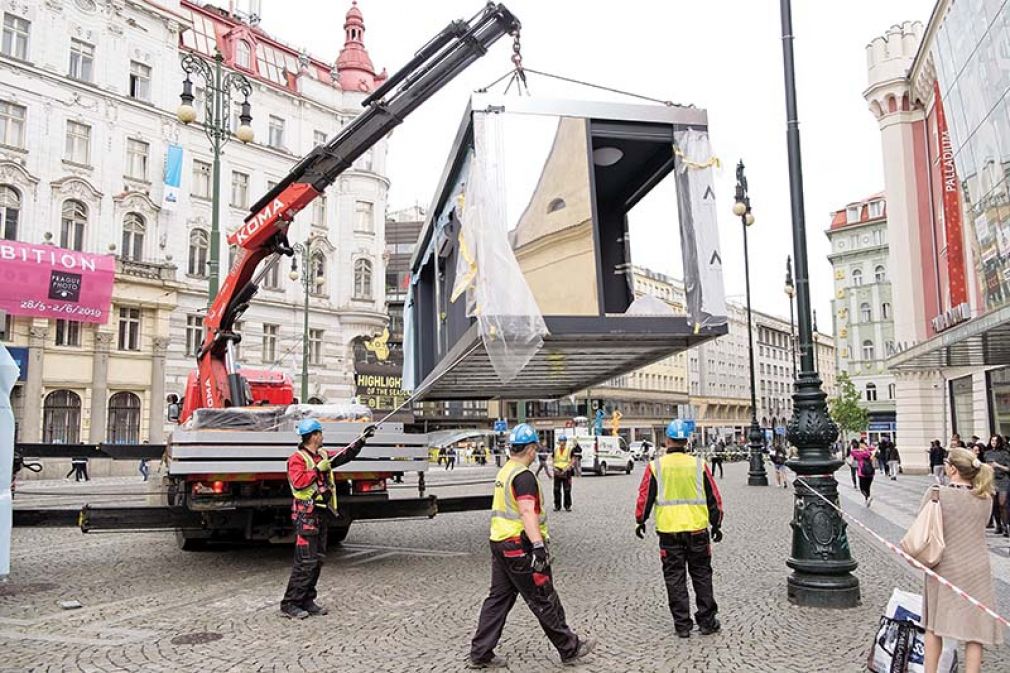
In der Automobilindustrie längst Usus, bietet Fließbandfertigung auch für den Bau großes Potenzial. Die Systematisierung ist effizient, spart Zeit und Kosten und bildet einen Ausweg angesichts kontinuierlich steigender Baukosten und akutem Wohnraumdefizit.
Die Baubranche spricht seit vielen Jahren davon, dass sie sich etwas von der industriellen Serienfertigung abschauen möchte«, sagt Thomas Belazzi, Geschäftsführer von bauXund. Mit der modularen Bauweise und der Verlagerung der Produktion in Fabrikshallen bietet sich ein effizienter Baustein, Bauzeit zu verkürzen und Bauqualität zu erhöhen. Zeit- und Ablaufpläne sind genau kalkulierbar, die Unfallprävention wird erhöht, und das Improvisieren auf der Baustelle entfällt.
Eine Minimierung von Informationsverlusten zwischen den einzelnen Projektphasen, digital durchgängige und, wo sinnvoll, automatisierte Prozesse bilden laut Habau das Fundament der Projektabwicklung. Module, etwa ein Zimmermodul oder eine Nasszelle inklusive Armaturen und Duschwanne, können in der Fabrik gefertigt, auf die Baustelle geliefert und dort verbunden werden. Damit entsteht aber kein Zwang zu 0815-Strukturen. Univ.-Prof. Gottfried Mauerhofer vom Institut für Baubetrieb und Bauwirtschaft an der TU Graz, berichtet von einem Besuch bei einem Hersteller von Holzmodul-Elementen. »Er bietet 300 verschiedene Varianten, ohne dass für ihn große Rüstzeit entsteht.«
Bild oben: Ziel der Strabag ist laut Vorstandsmitglied Peter Krammer die Minimierung der Verschwendung und die Maximierung der Produktivität. Dafür braucht es eine möglichst umfassende Vorfertigung im Vorfeld der Montage auf der Baustelle.
Argument Raumstruktur
Modulares Wohnen, d.h. das Maximum von Vorfertigung, eignet sich v.a. für den Wohnbau, Hotels oder Spitäler, weil die Raumstrukturen von den Größenordnungen her im Unterschied zum Industrie- und Gewerbebau ähnlich sind. Das amerikanische Vorzeigeunternehmen Katerra spricht von Mass Customization mithilfe modularer Elemente. 90 Prozent der Holzbaumodule sind vorgefertigt. Auch in Österreich setzen einige Unternehmen laut AEE Intec bereits auf Modulfertigung, im Holz- wie auch im Betonbau. »Vielfach, vor allem am Land, ist aber noch verankert, dass die schnelle Bauweise billig und damit nicht so lange haltbar ist«, bedauert Karl Höfler von AEE Intec.
In Großstädten sei modulares Bauen schon eher Thema. Michael Wardian, Spartenleiter Kirchdorfer Concrete Solutions, ergänzt: »Die Zukunft der Bauindustrie braucht mehr Standardisierung sowie Digitalisierung der Planung, Abläufe und der Vorproduktion, um weiterhin auf hohem Niveau agieren zu können. In Österreich bauen wir sehr individuell, was der Digitalisierung in der Bauproduktion gewisse Grenzen setzt.«
Angepasster Bauablauf
Bis auf die Baustellenvorbereitung und die Herstellung der Fundamente, die weitgehend konventionell erfolgt, ist die Logistik eines Modulbauers eher mit der Autoindustrie vergleichbar. »Wir produzieren, liefern und montieren just-in-time. Dadurch können wir den Platzbedarf sowohl in der Lagerung wie auch auf der Baustelle auf ein Minimum reduzieren und die Kosten niedrig sowie die Zeitpläne einhalten,« berichtet Stanislav Martinec, Firmengründer und CEO bei Koma Modular, der sich schon seit 25 Jahren mit der Problematik des modularen und temporären Bauens beschäftigt.
Auf der Baustelle werden nur noch die Verbindungen unter den einzelnen Einheiten hergestellt. Wasser, Strom und sonstige Leitungen sind so weit vorbereitet, dass ein einfaches Verbinden miteinander sowie mit dem örtlichen Netz möglich ist. Digitale Daten und Automation sind der Schlüssel für die Erstellung und effektive Zeitplanung im Werk. Im Bauablauf muss zwischen Gebäude- und Bautechnik koordiniert werden, auch zeitlich.
»Die herkömmliche Baulogistik wird neu aufgestellt«, informiert Frank Otters, Vertriebsleiter für modulares Bauen bei Lechner Immobilien Development. Zunächst müsse der Fertigstellungstermin als verbindliches Ziel fixiert werden. Davon ausgehend werde, rückwärts rechnend, die Produktion, die Beschaffung und die Herstellung des Baurechts vorbereitet.
Bild oben: Die kontinuierlich steigenden Baukosten und das akute Wohnraumdefizit fordern neue Lösungen.
Modulare Planung
Die Baumodule werden aufgrund des hohen Vorfertigungsgrades detaillierter geplant als bei konventioneller oder serieller Bauweise üblich. Dies geschieht unter Zuhilfenahme von BIM. Anhand des Gebäudemodells werden die Werkpläne der einzelnen Module erstellt. Frank Otters berichtet vom modularen Bauen mit Stahlbeton. In der Deutschen Modulhausfabrik werden komplette Raummodule aus Stahlbeton produziert. Der Vorfertigungsgrad liegt über 90 Prozent.
Blickwinkel Holz »Die vorgefertigten Elemente werden so in den LKW oder Container eingeladen, dass sie in der richtigen Reihenfolge ausgeladen und sofort aufgebaut werden können«, beschreibt Johanna Kairi, Business Development Manager beim größten europäischen Holzverarbeiter Stora Enso. Mittels Track & Trace Tools kann die Lieferung verfolgt werden. Auf der Baustelle ermöglicht die App CLT360 eine Übersicht der Anordnung der Elemente im Gebäude. Stora Enso entwickelt im Labor digitale Werkzeuge, die das Zeichnen, Planen, Ausmessen und Berechnen vereinfachen.
Die Idee von Katerra
Katerra fertigt Holzhäuser in Modulbauweise. Dabei übernimmt ein einziges Team alles vom Blueprint bis zur Materiallieferung, Vernetzung der globalen Lieferkette mit BIM und Computerdesign.
- Fabriken und Baustellen werden verknüpft, geliefert wird just-in-time.
- Standardisierte Bauteile sparen Zeit und damit Geld.
- Die Digitalisierung der Lieferkette erspart Mittelsmänner, das bedeutet ein großes Einsparpotenzial.
- Mit dem im Bauprozess eingesparten Geld werden weitere Fertigungsfabriken eröffnet werden.
Serienfertigung bei Lechner Immobilien Development
Der Herstellungsprozess des Systems Modularer Massivbau orientiert sich maßgeblich an der Automobilindustrie, gefertigt wird in drei Phasen:
1.Phase: Erstellung des Stahlbewehrungskorbs der Module mit Aussparungen für Fenster, Türen und Raumöffnungen Einbringen von Elektro-Kabelsträngen, Leerrohren sowie Leerdosen für Elektro- und Multimedialeitungen, Fußbodenheizungs- sowie Sanitärleitungen, Zusammenführen der Leitungsenden im Revisionsschacht
- Verfahren der raumumschließenden Bewehrungskörbe inkl. der Leitungen für Heizung, Sanitär und Elektro auf einer Palette in die Modulschalung, Aussparungskörper für Fenster und Türen sind angebracht. Fixierung der Position der Elektro-Leerdosen, Schließen der Schalung, Einbringen und Verdichten des Betons
- Aushärten des Betons durch Wärmezufuhr, Verfahren der Schalung auf Palette
2. Phase : Erweiterung des Moduls auf der Produktionsstraße, beginnend mit dem Innenausbau:
vorgefertigte Installationswände, Anbringen der Kupplungen für Stecksysteme im Plug+Play-Verfahren, Vorbereiten für die Verbindung der Anschlüsse bei der Montage auf der Baustelle, Fenstereinbau, Herstellung der Außendämmung, Anbringen Außengrundputz und ggf. Dachabdichtungen. Sicherung der Module und Zwischenlagerung
3. Phase :Transport der Module per Schwerlasttransport auf die Baustelle
- Montage mit 220 t-Kran und Kopplung untereinander. Pro Montage-Kolonne können zehn Module pro Tag (ca. 200–240 m² WoFl) montiert werden.
- Arbeiten auf der Baustelle: Außenanlagen, Erschließung bzw. Hausanschluss, WDVS im Sockelbereich zwischen Modul und Bodenplatte, Oberputz, Tür- bzw. Durchgangszargen zwischen den Modulen, Bodenbeläge im Übergangsbereich der Module sowie Anstecken des Dachterrassengeländers
Bauablaufstörungen vermeiden
Eine nachhaltige Entwicklung kann laut Habau flächendeckend nur dann gemeinsam bewerkstelligt werden, wenn der Fokus auf den gesamten Bauprozess und auf eine moderne und abgeschlossene Planung gelegt wird. Damit könnten laut Hubert Wetschnig, CEO Habau Group, viele Ursachen für Bauablaufstörungen eliminiert werden. »Schnittstellen und mögliche Planungsänderungen können in einer frühen Projektphase in einem sogenannten Koordinationsmodell mit standardisierter Kollisions- und Attributsprüfung transparent und nachvollziehbar aufgezeigt und rasch zwischen den betroffenen Fachplanern abgestimmt werden.«