Wiederverwendung von Tunnelausbruchmaterial
- Written by Redaktion
- font size decrease font size increase font size
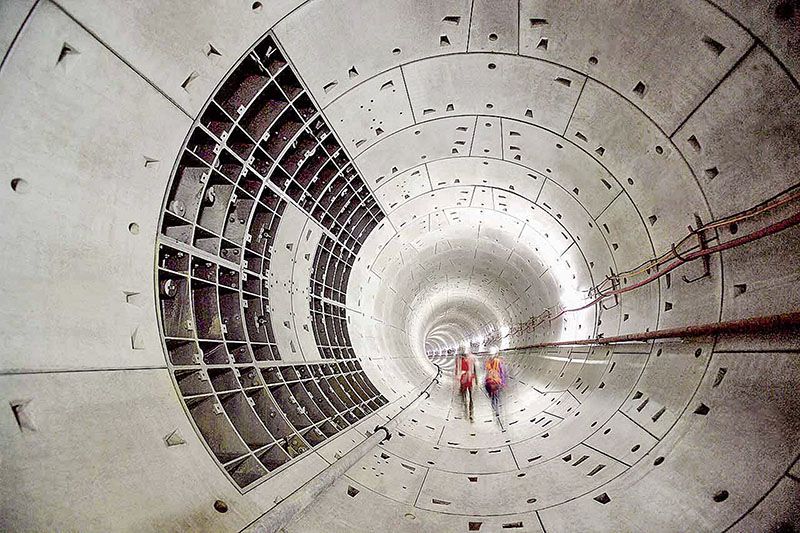
Die Wiederverwendung von Tunnelausbruchmaterial für die Herstellung von Gesteinskörnungen spielt bei großen Infrastrukturprojekten eine immer größere Rolle. Ein kurzer Streifzug durch die Materialaufbereitung aus Sicht des Tunnelbau-Unternehmers, welche Rolle IRIS spielt und wie die Zukunft aussehen wird.
Die Autoren:
- Dipl.-Ing. Maximilian Apfelbaum – Strabag AG / Unternehmensbereich Tunnelbau
- Ing. Stefan Bruckman – Strabag AG / Unternehmensbereich Tunnelbau
- Dipl.-Geol. Christian Deckert – Strabag AG / Unternehmensbereich Tunnelbau
- Baurat h.c. Dipl.-Ing. Dr. Helmut Huber – Sachverständiger
Grund und Boden sind besonders im Alpenraum sehr begrenzte Ressourcen. Im Zuge großer Infrastrukturprojekte wird daher auf Grundlage des allgemeinen sozialen Ansatzes während der Planung eine maximale Wiederverwertbarkeit von Tunnelausbruchmaterial unter Berücksichtigung der Geologie, Wirtschaftlichkeit, rechtlicher Rahmenbedingungen und einer möglichst geringen Umweltbelastung angestrebt. Diese Situation stellt Auftraggeber, Planer und Baufirmen immer wieder vor große Herausforderungen. Strabag verfügt über die Erfahrung bei der Materialaufbereitung, um bei der richtigen Geologie bessere Betonrezepturen herstellen zu können. Für die Verwendung von kristallinem Tunnelausbruch liegen jahrzehntelange Erfahrungen vom Bau der großen Kraftwerksanlagen im Alpenhauptkamm vor. In den Jahren 1950 bis 1990 wurden insbesondere in Österreich und der Schweiz die Betone der hohen Talsperren, hochbeanspruchter Triebwasserstollen und Kraftstationen mit aufbereiten kristallinen Gesteinskörnungen aus Tunnelausbruch oder Steinbrüchen mit Glimmergehalten bis über 35 Prozent hergestellt. ¹
Großbaustelle Koralmtunnel – KAT 2
Seit Beginn des neuen Jahrtausends war Strabag maßgeblich an großen Tunnelbauvorhaben wie zum Beispiel am Lötschberg und am Gotthard Basistunnel beteiligt. Die gesammelten Erfahrungen dienten auch beim Projekt Koralmtunnel – KAT 2 als wertvolle Grundlage für die weiteren Entscheidungen zur Wiederverwertung des Tunnelausbruchmaterials. Darüber hinaus zählt Strabag auch im Gesteinsabbau zu den führenden Unternehmen. Mittels innovativer Technik und Erfahrung werden Gesteinskörnungen von hoher Qualität hergestellt. Mit rund 200 eigenen Steinbrücken und Kiesgruben kann die optimale Versorgung mit hochqualitativen mineralischen Rohstoffen garantiert werden. Außerdem konnte die Strabag die Schnittstelle zu BIM beziehungsweise der digitalen Visualisierung mit der internen Lösung IRIS schließen. Dieses integrierte Risiko- und Informations-System IRIS ist ein innovatives System zur Risikosteuerung und Informationsgewinnung in Infrastrukturprojekten. Es erlaubt einen web-basierten Zugriff auf alle relevanten Projektinformationen und integrierte Datenanalyse sowie leistungsfähige Visualisierung in einer Plattform. Das Softwaresystem IRIS wurde von dem Team ITC Engineering entwickelt und wird zusammen mit den Kunden für jeden Baustellentyp projektspezifisch ausgearbeitet.
Im Zuge jedes Projektes durchläuft das Ausbruchmaterial eine Vielzahl von unterschiedlichen Orten, an denen es temporär oder länger gelagert wird beziehungsweise einer anderen Verwendung zugeführt werden muss. Hierbei ist ein effizientes Monitoring über den Mengenstrom, aber auch über die Streckenförderbänder erforderlich. Der Einsatz von IRIS hat die Möglichkeit geboten, die Wege von Ausbruch- und Entsorgungsmassen schneller und effizienter zu erfassen. Andererseits ergibt sich dadurch eine transparente Dokumentationsgrundlage für den Deponiebetrieb.
Das Projekt im Detail
Im Zuge des Bauloses KAT 2 wurde der Auftragnehmer mit einer Gesamtlänge von 38,2 km Streckenröhren, Querschlägen und der Nothaltestelle beauftragt. Hierbei werden insgesamt 8,6 Mio. Tonnen Tunnelausbruchmaterial (polymetamorphe kristalline Gesteine) anfallen; diese müssen durch den Auftragnehmer entsprechend aufbereitet beziehungsweise deponiert werden. Die Arbeiten sind weit fortgeschritten. Die Strabag hat hierfür die Materialaufbereitung in Eigenleistung zur Herstellung von Gesteinskörnungen für Beton realisiert und war die federführende Firma bei der Umsetzung der Kiesaufbereitung.
Die angetroffene Geologie im kontinuierlichen Vortrieb befindet sich vollständig im metamorphen Gestein. Bis Oktober 2014 wurden Gesteine der Glimmerschiefer-/Schiefergneisfolge aufgefahren. In diesem Abschnitt dominieren Schiefergneis und Glimmerschiefer; untergeordnet befinden sich Gneise, verschiedene Marmore, Amphibolit und vereinzelt Linsen von extrem abrasivem Eklogit. Nennenswerte Bergwasserzutritte wurden, außer in einer Störungszone mit Marmor, nicht angetroffen.
Aus diesem Zusammenhang stellt der hohe Glimmeranteil gemäß der Lithologie am Projekt KAT 2 zum Teil über 40 Prozent im Abschnitt der Glimmerschiefer-/Schiefergneisfolge eine besondere Herausforderung dar. Bei extrem hohem Gehalt an Glimmer muss aus betontechnologischer Sicht das Material ausgeschieden werden. Diese Situation ist keine ideale Vorausetzung für die Herstellung von hochwertigen Tübbingbetonen. Seit November 2014 wurden Gneise aufgefahren, die eine hohe Festigkeit und Abrasivität aufweisen. Dieses Gestein eignet sich sehr gut für die Herstellung von Kornfraktionen für die Betonproduktion. Die Tunnelvortriebsmaschine (TVM) zerlegt den Gneis mit seinem Schneidrad und bricht plattige Chips mit hohem Gesteinsmehlanteil heraus.²
Um den sehr hohen Anforderungen der Wiederverwertung von Tunnelausbruchmaterial gerecht zu werden, wurde für das Baulos KAT 2 ein weitläufiges und komplexes System der Materialaufbereitung entwickelt (siehe Foto oben). Der Prozess der Materialaufbereitung beginnt bereits in unmittelbarer Nähe des Tunnelvortriebes am Nachläufer der Tunnelvortriebsmaschinen (TVM). Dort wird das geförderte Tunnelausbruchmaterial auf einen Korndurchmesser von max. 150 mm zerkleinert, um Schäden an den Förderbändern zu vermeiden. In weiterer Folge wird das Material über bereits aufgefahrene Streckenröhrenabschnitte zum Versorgerschacht auf der Baustelleneinrichtungsfläche KAT 2 (Leibenfeld) transportiert, wo es mittels Senkrechtförderanlage an die Oberfläche gelangt.
Die Qualität entscheidet
Grundsätzlich wird nur jenes Ausbruchmaterial zur Gewinnung von Gesteinskörnungen von 0–32 mm herangezogen, das auch bezüglich seiner Zusammensetzung dafür geeignet ist. Materialien, die etwa aufgrund eines zu hohen Feuchtegehalts oder minderer Qualität für die Zuführung zum Aufbereitungsprozess nicht geeignet sind, werden vor der Siebanlage an einer Abwurfeinrichtung ausgeschieden, einer Deponie zugeführt oder abtransportiert. Verwendbares Material wird mittels Förderbändern einer Vorsiebanlage beziehungsweise Siebturm zugeführt, wo ein Trennschnitt von 16 mm (projektspezifisch) erfolgt.
Das von Feinteilen (< 16 mm) getrennte Material wird per Streckenförderer der eigentlichen Materialaufbereitungsanlage beziehungsweise Kiesaufbereitung zugeführt. In diesem Prozess wird das Tunnelausbruchmaterial über mehrere Brecherstufen zerkleinert sowie kubifiziert und gelangt dann in Siebmaschinen, wo es intensiv mit Wasser bedüst wird. In der Siebanlage wird zum einem die Sandfraktion 0/3 mm getrennt, zum anderen werden die Fraktionen 3/8, 8/16 und 16/32 konfiguriert. Die Sandfraktion 0/3 mm wird in Freifallklassiertanks gelagert, in Unterfraktionen aufgeteilt und anschließend entwässert. Die so hergestellten Gesteinskörnungen werden der Betonproduktion zugeführt.
Ein langer Weg
Bei der Konzepterstellung der Materialaufbereitungsanlage im Jahr 2012 wurden am Beginn zahlreiche Versuche mit Ausbruchmaterial aus dem zyklischen Vortrieb mit unterschiedlichen Brechertypen durchgeführt. Neben Verschleiß und Betriebskosten waren die durch die Brecherkonfiguration erzielbare Kornform und die Kornverteilung wesentliche technische Kriterien. Die qualitätsgesicherte Produktion der Gesteinskörnungen wurde in der Materialaufbereitungsanlage (»KiAu«) ab Juli 2013 begonnen. In den nachfolgenden Jahren, bis Ende Dezember 2016, wurden rund 721.000 Tonnen Gesteinskörnungen erzeugt beziehungsweise 550.000 Tonnen in der Betonproduktion für die Herstellung von Betonfertigteilen für Tübbinge und Sohlelemente beziehungsweise Innenschalenbeton für die Querschläge und Spritzbeton verwendet.
Es wurde ein monatlicher Produktionsspitzenwert im Februar 2014 von knapp 30.000Tonnen erzielt.
Der restliche Innenausbau der Streckenröhre (Innenschale, RBS-Platte), Querschläge und der Nothaltestelle folgt nach Vortriebsende. In der Betonproduktion wurden bisher 550.000 Tonnen Gesteinskörnungen aufbereitet und großteils für Normaltübbinge beziehungsweise Sohlelemente mit den Druckfestigkeitsklassen C35/45 verwendet. Die Fertigteile werden auf der Baustelle in zwei Tübbing-Werkshallen selbst produziert.
Außerdem mussten im Zuge der Vortriebsarbeiten Spezialtübbinge beziehungsweise gesonderte Spezial-Sohlelemente mit den Druckfestigkeitsklassen C50/60 für Sonderbereiche in den Streckenröhren hergestellt werden. Diese Fertigteile mussten jedoch aufgrund der Nicht-Eignung der Schiefergneise und Glimmerschiefer mit extern angelieferten Gesteinskörnungen produziert werden.
Zusammenfassung und Ausblick
Die Bauindustrie in Österreich mit ihren Forschungseinrichtungen beschäftigt sich schon seit vielen Jahrzehnten sehr intensiv mit der Wiederverwendung von Ausbruchmaterial und bietet die Möglichkeit, ressourcenschonende Projekte realisieren zu können. Strabag hat eine Vorreiterrolle auf diesem Gebiet eingenommen, um neben Nachhaltigkeitskriterien und Umweltaspekten auch die wirtschaftlichen Vorteile in der Praxis umzusetzen.
Dabei erweist sich die gewählte und leistungsstarke Kiesaufbereitungsanlage als sehr wichtiger Erfolgsfaktor. Hierbei muss sehr genau auf die Vorabsiebung und Materialaufbereitung eingegangen werden, um mit den wechselnden Eigenschaften des Rohmaterials umgehen zu können. Am Beispiel der Baustelle KAT 2 traten im Tunnelausbruchmaterial – wie eingangs erwähnt – relativ hohe Glimmergehalte auf.
Gleichzeitig gab es im Zuge dieses Projekts die Anforderung, Tübbinge mit hohen Betondruckfestigkeitsklassen C50/60 herzustellen. Für die Tübbingproduktion mit hohen Anforderungen an die Druckfestigkeitsklasse C50/60 können bei petrografisch ungünstig verteilten Glimmergehalten oder reduzierten Gesteinsfestigkeiten bei Glimmerschiefern oder Schiefergneisen nur höherwertige externe Gesteinskörnungen eingesetzt werden. Der Grund liegt im erhöhten Bedarf an Zement beziehungsweise Bindemittel und weiteren Additiven, was für die Betonproduktion unwirtschaftliche Auswirkungen hätte (höhere Bindemittelgehalte würden die CO2-Bilanz des Bauprozesses wiederum negativ beeinflussen). Die mineralogische Zusammensetzung der Kornfraktionen beziehungsweise die Form und Gesteinsfestigkeit sowie der Wassergehalt haben eine entscheidende Rolle für den weiteren Aufbereitungsprozess unter Berücksichtigung der technischen und wirtschaftlichen Machbarkeit. Die herausfordernde Situation ist die Auswahl von brauchbarem Tunnelausbruchmaterial.
In Fortsetzung und ständiger Weiterentwicklung der Kiesaufbereitungsanlage und der bestehenden Erfahrungen hinsichtlich der Verwendung kristalliner Gesteine für die Betonerzeugung konnte Strabag über den gesamten Aufbereitungszeitraum für das Baulos KAT 2 sehr gute Ergebnisse erzielen. Hinzu kommt, dass die Energiebilanz und der damit verbundene CO2-Ausstoß durch die Wiederverwertung von Tunnelausbruchmaterial im Vergleich zur Deponierung viel niedriger sind.
Quellenverzeichnis:
1] Huber, H., Kratochwill, R. Otto, R.: Use of recycled material for segments and inner lining – first experience of on site processing on KAT2/ Verwendung von Tunnelausbruchmaterial – von der TBM bis zum Tübbing, erste Erfahrungen mit der Materialaufbereitung vor Ort im Baulos KAT2. Geomechanics and Tunnelling No. 6 (2013), pp. 661–668
2] Posch, H., Otto, R., Huber, H., Murr, R. Kager, M., Wagner, H.: Recyling of tunnel excavation using the example of the Koralm Tunnel, contract KAT2 – Status April 2015 / Verwertung von Tunnelausbruch am Beispiel des Koralmtunnels, Baulos KAT2 – Stand April 2015. Geomechanics and Tunnelling No. 4 (2015), pp. 340–347